加工精度が劇的向上!ホルダー選定で加工時間を半減に!
サービス範囲 | 現状確認→機種選定→デモ機貸出→お見積 |
---|---|
施工内容 | 治具選定 |
内容
機械加工において、ホルダーは工具の性能を最大限に引き出すための重要な要素です。特に高精度な加工が要求される金属加工では、ホルダーの選定が製品品質に直接影響を与えることが多くあります。今回は、ホルダー選定の一例として、EU規格のホルダーチャック「ファーリオン」をご紹介します。
適切なホルダーを選ぶことで、工具の振動(ビビり)を抑え、加工速度の向上や製品精度の安定化が期待できます。
今回は、ホルダー選定の一例として、EU規格のホルダーチャック「ファーリオン製コレットチャック」をご紹介します。
【Before】
従来のホルダーには「隙間」があり、これが工具のビビりの原因となっていました。このビビりが加工精度の低下や、作業効率の悪化につながっていました。そこで、ファーリオン製コレットチャックを提案しました。このホルダーは隙間がない構造で、ビビりが大幅に抑制されることが特徴です。さらに、従来の日本製ホルダーと比べて機械との相性も良く、加工速度の向上が期待できました。
【After】
提案に基づいて、ファーリオン製のホルダーをデモ機として1ヶ月間使用頂いた結果、約5000穴の加工時間が従来の65時間から30時間に短縮されました。この改善は他の工具の見直しも含まれるものの効果の8割以上がホルダーの交換によるものでした。
ファーリオン製のホルダー「コレットチャック」のご紹介
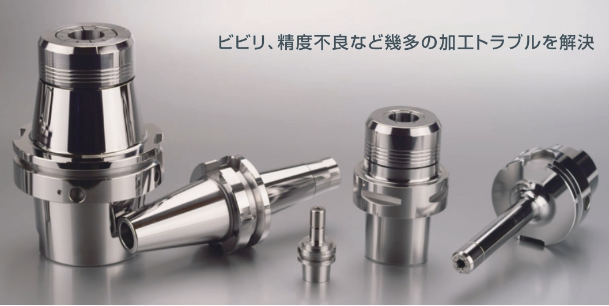
今回選定しましたファーリオン製のホルダー「コレットチャック」の特長をご紹介します。
①独自デザインによる高剛性
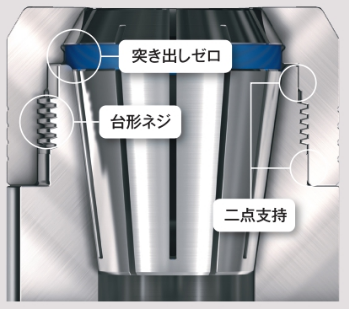
コレット、本体、ナットの間に隙間を一切生じさせない独自設計を採用しています。さらに、山ねじではなく台形ねじを採用し、二点支持構造により、部品同士が確実に密着する仕組みとなっています。
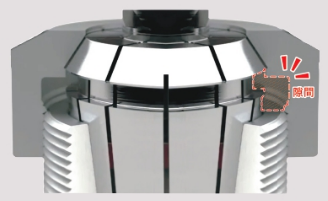
従来のコレットチャックでは、本体とナットの間に微細な隙間が存在することが一般的です。この隙間が原因で、部品同士の剛性が低下し、ビビり振動が発生しやすくなります。
②コレット突き出しゼロ
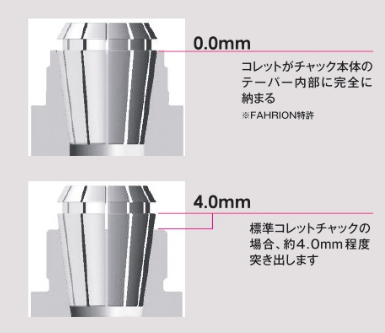
コレットの据わる位置が安定することで、工具の取り付けにおける繰り返し精度が向上します。これにより、どなたでも簡単に最適な振れ精度に調整できるため、工具セットに要する時間が短縮され、作業効率の向上が図れます。
今回選定しました、このセントロPチャックは、内径テーパーに完全に収まるよう設計されています。従来型チャックでは、デザイン上どうしてもコレットが2~4mm程度突き出してしまい、これが加工時の不安定さや把握力の低下を引き起こす要因となっていました。しかし、セントロPチャックでは「コレットの突き出しゼロ」および「本体・ナットのネジ設計見直し」により、高い剛性と優れた振動減衰効果を実現。これにより、加工時の振れ精度が向上し、工具費用の削減と生産性の向上に大きく貢献します。
本件はホルダーの適切な選定が加工精度と作業効率い大きな影響があるという事例でした。工具だけでなく、ホルダーなどの付属品にも目を向けることでより効果的な加工改善が可能となります。もし同様の課題をお持ちの方は、一度ホルダーの見直しを検討してみてはいかがでしょうか?ファーリオン製ホルダーはデモ機の無料貸し出しも可能ですので是非ご利用ください。